WORKBOAT FENDER SYSTEMS
I - GENERAL DATA
OCEAN 3 's Workboat Fender Systems will give you a peace of mind during berthing manoeuvers. They are manufactured from 2 high quality materials :
- Polyethylene Foam (PE) which provides high energy absorption and low reaction force
- Polyurethane coating (PU) which is reinforced with multiple layers of textile to increase both the tear and abrasion resistance.
The calculation of kinetic energy which needs to be dissipated is based upon the following parameters :
- Boat specification/characteristics (Length, Width, Draft, full laden Displacement,...)
- Condition of use (Pilotage, Patrol, Crew Transfer,...)
- Section/Shape requirements (Cylindrical, D-Shape, Return on Deck, Squared, Rectangular...)
- Fixing Method (Strapped, Glued, Bolted, ..., or mixed)
- End use (Harbor Operations, Boat Landing :Crew Transfer, Side Berthing...)
- Berthing speed.
Starting from a Naval architect drawing or customer supplied GA, our Technical Team determine and implement the best compromise of all parameters after initial design calculation. The earliest these parameters are considered in the project, the best suitable solution and most economic system will be.
The Fendering Systems can be either individual partial sections or complete all around the boat, according to use and budget.
The Fenders tend to be called "composites" because their functions are dissociated : the foam core acts as a shock absorber during berthing. The Polyurethane coating will also increase the Energy dissipation efficiency via the encapsulation of the Foam Core but also provides high abrasion resistance for long life span. All OCEAN 3 workboat Fender Systems are taylor made to the nearest centimeter in all measurements according to the Energy calculations and the End User requirements.Tha shape of our Fenders is often related to the required fixing mechanism as follows :
II - TYPOLOGY OF WORKBOAT FENDER SYSTEMS
- 1. Strapped in a "V" recess made in the Hull, this is a typical fixing methodfor our cylindrical Fender sections. Or located between two D shaped profiles, squarred or rectangular sections in order to contain the vertical forces during berthing operation (Hard berthing, Crew transfers...). An additional through wire cable can be inserted through the fender to keep the modules in place in case of strap damage.
RECESS FOR CIRCULAR SECTION FENDER
RECESS FOR COMPLEX SECTION FENDER
2. Bonding using Adhesives (Sikaflex type). Typical for D-Shaped, Squaree or Rectangular Fender sections which have a flat back and follow a flat section along the Boat Hull. A through wire cable can also be added to ensure fixation in case ofglue failure.
GLUED SECTION DELTA
DELTA SECTION WITH RETURN ON DECK
- 3. Bolted mechanism : this can be proposed in cases where a recess cannot be made in the Hull to take a cylindrical shaped Fender and/or if gluing is not permissible. In that particular case, Fenders have a steel plate inserted into the Fender in order to either bolt through the inside or the outside of the Boat Hull. Also a Fender can be bolted vertically in certain cases and if we have allowed for this.
Depending on the admissible total pressure which can be taken by the hull, the foam densities vary from 18 to 200 Kg/m³ (And beyond if required), in order to calculate required amount of Energy against a certain given volume of foam. Foam densities can be increased or even "hardened" in specific stressed areas of the Boat, or even a single Fender can also be composed of several densities of foam according to condition of use (Bow Fender for Boats used as Tug for instance). By playing around with the varying foam densities, it allows our fenders to dissipate higher Energt whilst keeping the same dimension of Fenders.
The coating thickness ranges from 5 to 40 mm (Even more if required) according to the use or targeted lifespan, and includes reinforcements with textiles, fabrics or fibers (metallic or synthetic).
Foam filled Fendering will provide many advantages compared to traditional systems, such as inflatables tubes or compared to Rubber D profiles :
- No risks of puncture and total failure
- Lower weight and higher Energy absorption
- Fenders go on working even if punctured or damaged
- No Maintenance required through pressure checking or variations of pressure due to changing ambient temperatures.
- Coating reinforced with no propagation of tears, even if damaged.
- More proportional to Kinetic Energy absorption.
- Bringing no damage even if used beyond admissible compression.
- No shocks transmitted to the Hull
III - Composition of Workboat Fendering Systems
A) Bow Fenders
They will be manufactured exactly as per the shape of the Bow and follows its contour. It is intended to protect the front of the Boat and can be partial or as part of a full complete equipment, or for Tug use. The Ends can be beveled down, angled, snaped or reduced in diameter or decreased conically. Cuff and spigot joints (Male/Female) can be madeshould it be necessary.
B) CURVED FENDERS
When as part of a complete set, they are sometimes equipped with a cuff-and-spigot for cylindrical section, or straight ends for a "Delta" type section. Single unit Curved Fenders can be made just to "beef up" and protect the Shoulders and Aft Corners of the Vessel when multiple side berthing operations are performed (Typical of a Pilot Boat use). These modules can be "hardened" by use of higher foam densities.
C) STRAIGHT FENDERS
Those are the modules located between the Bow Curved and Aft Corners Fenders; their utility is only for the continuity of the full equipment. They can terminate with Cuffs/Spigots and a hose in the center for passing through safety wire as an option. Their other role, especially in isolated use, is to act as a "relayed" protection when the gap between the Bow and Aft Corner Fenders is too important to have a continuous protection; they will then act as a further protection to the Boat Hull. These Fenders are often made with a lower Foam density as their role is not as important; to save both cost and weight.
D) REAR / STERN FENDERS
For full equipments, Rear Fenders are equipped with either Cuffs/Spigots or as a solid ends; termination of these modules on transom is generally 1/2 sphere; they can have a hose in their center to pass a through safety wire. They may stop at the corner of the boat, or have a return on transom, partial or continuous. This return is recommended to protect the Aft Corners of the Boat when the Boat leaves from its berthed position.
IV - ACCESSORIES
A) STRAPS
Straps are the most widely used mean of fixation for Workboat Océan 3 fendering system. Other means of fixation are gluing with PU mono or bi component PU based Glue, less often bolting or other combination of some of these solutions
In case of fenders strapped or glued on the hull, a wire can be added, passing thru all fenders by polyethylene hose in the middle of fenders, and tightened out of them to avoid to loose one module in case of severe shock
Straps are equipped with 2 or 3 buckles of « Delta » type; made out of 316L stainless steel, Thread diameter Ø 10 mm to Ø 14 mm. Buckles are passivated under electrolytic process to prevent sea water oxidation
Less high type buckles allow fender to be compressed a bit more without risks of buckles to get in contact with hull, especially for lower diameter fenders.
Seam of buckles on straps is operated by sewing robots (for good regularity) in crenulations way (for thread to be inserted in structure of strap) not to submit thread to previous abrasion and premature breaking of sewing
Tensile strength of strap is around 8 Tons, sewing (number of stitches) is calculating to pass tensile strength of strap, distortion of buckles starts when submitted up to 2,5 Tons to break around 5,5 Tons
3 buckles straps bring axial withstanding for fenders and avoid them to slide to the stern when rubbing alongside a quay or other boat
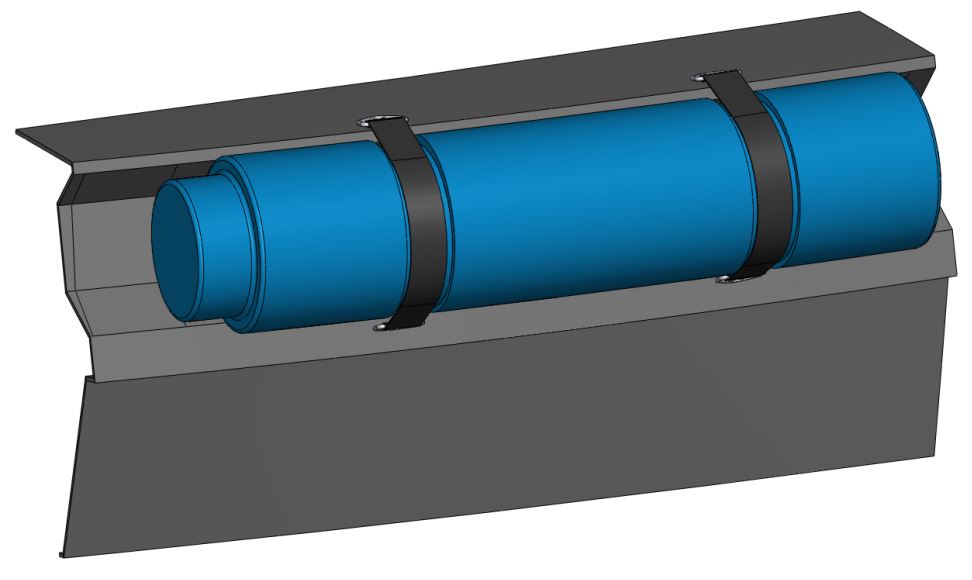
2 Buckles straps can be inserted in grooves to preserve them a bit more from rubbing or being “hooked” by protruding things. Usually manufactured in dark grey colour, they can be also realised in more visible colours if necessary (Bright yellow, Orange or else…)
These « handling type » straps present high abrasion resistance due to textile structure and material. Weaving and material : polyester, bring low friction coefficient, and great resistance to chemical products and to weather conditions exposure (UV, sea water,…) They can be coated with additional abrasion layer of casted HAR PU 95 ShA, same kind of fender coating. At OCEAN 3 straps are coated by High Injection Molding Process to bring best bonding to the strap.
Straps are moored to hull chain plates by the mean of shackles at lower parts and tensioning system at upper parts or on deck (Jack rope, turnbuckle, or others) Jack rope is main used system and very simple to fit; It could be considered as fuse in bonding to avoid if strap is « hooked » anchoring points or hull to be damaged
High resistance Polyethylene rope « Spectra » or « Dyneema », UHMWPE type, preferably PU coated (firmly avoid mesh knitted sheath that would slide) or pre-tensioned polyester Ø 5 to 8 mm. Restrict number of round with jack rope, between upper buckle and deck chain plate, to 4 for High resistance polyethylene (Ø 5 to 6 mm) to avoid the “fuse” to be the strap instead of jack rope usually considered so; and to 6 for pre tensioned polyester (Ø 6 to 8 mm)
Duration life of straps obviously depends on use, rubbing frequency of the Ocean 3 Workboat Fender Systems and roughness of reaction berthing surface in contact with textile or protective coating. Nevertheless experience allows us to consider duration before changing of straps, or refurbishment every 3 to 7 years according to previously mentioned elements (approx. 5 years for Pilots with mean of 5000 hours of use per a year).
Always rightly tensioned straps increase their duration of life notably. With new set of fender, when fitted for 1st time on the boat, it is often necessary to proceed to re-tensioning of straps after a period of test for workboat, due to repositioning of fender in recess.
Tensioning of straps is easier with use of simple tensioning tool, hooked both in upper buckle and deck chain plate : 1 meter length approx. lever arm allowing to bring together these 2 elements, time to twist jack rope or place pre-tensioned shackle, before releasing tension (Tensioning tool arrangement on simple request)
Easiest way to make the straps slide on the fender, during tensioning, is to put "soapy water" on side of strap in contact with Fender to move one from the other. Soapy water will disappear during first sailings and give back to the system its original bonding.